Share this
The Cost of Quality: How to Calculate and Reduce Hidden Costs
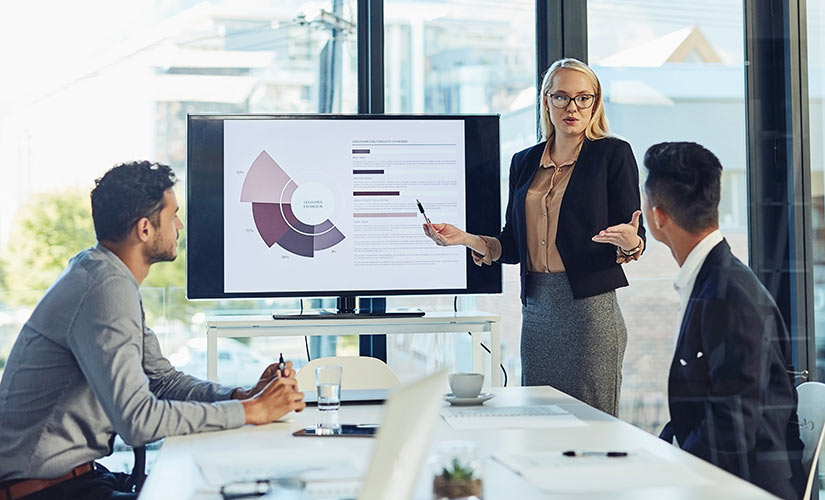
by QT9 QMS Software on July 21, 2025
For company decision makers, the cost of quality is not often seen as an opportunity, but rather as the cost of ensuring regulatory compliance. To measure this, businesses generally track the costs of obvious quality failures, like scrap, rework and product recalls. But the true cost of quality (CoQ) reaches far beyond these more visible outcomes.
For quality professionals, especially those in high-stakes manufacturing environments like life sciences and aerospace, getting a complete picture of quality-related costs can reveal a multitude of opportunities to not only meet regulatory standards, but to also increase efficiency, reduce risk and improve profitability.
This article explores the broader dimensions of the total cost of quality, breaks down how to best measure it and highlights how modern Quality Management Systems (QMS) like QT9 QMS can help tackle hidden costs and reveal potential opportunities.
Contents
The Cost of Good Quality (CoGQ)
The Cost of Poor Quality (CoPQ)
How to calculate the Cost of Quality (COQ)
Hidden costs of quality manufacturers overlook
Why understanding total cost of quality matters
How QMS software reduces the cost of quality
Understanding total CoQ for targeted improvement
What is the cost of quality?
The Cost of Quality (COQ) refers to all expenses incurred to ensure that a product or service meets safety and quality requirements. It includes:
- The cost of achieving quality
- The cost of not achieving quality
According to the American Society for Quality (ASQ):
“The Cost of Quality (CoQ) is a methodology that allows an organization to determine the extent to which its resources are used for activities that prevent poor quality, appraise quality and correct internal or external failures.”
CoQ typically includes four components:
- Prevention Costs
- Appraisal Costs
- Internal Failure Costs
- External Failure Costs
The Cost of Good Quality (CoGQ)
The Cost of Good Quality includes Prevention Costs and Appraisal Costs and are investments that help avoid problems before they happen. When added together, data gathered about each type of cost helps organizations understand how much they are spending on quality management efforts and, in turn, can offer insights on ways to better address problem areas.
Prevention costs
Prevention costs are expenses related to preventing defects before they occur, such as:
- Staff training on quality standards
- Document control systems
- Process improvement initiatives
- Preventive maintenance on equipment
Why it matters: A dollar spent on prevention can save multiple dollars in rework, warranty claims or recalls later. In highly regulated industries, prevention costs can be significant due to the high bar that must be reached for compliance. However, if you’re going to have quality costs – and you are – prevention costs are the most cost-effective in the long run.
Appraisal costs
Appraisal costs are costs for activities that inspect and verify product quality, such as:
- Incoming material inspections
- In-process inspections
- Supplier evaluations
- Quality assurance labor
While appraisal activities don’t prevent quality issues outright, they play a critical role in detecting problems early, ideally before products leave the factory floor.
Cost of Poor Quality (CoPQ)
The Cost of Poor Quality (CoPQ) pertains to costs associated with providing poor quality products or services. These are usually a result of defects or failures in products. There are two categories that make up CoPQ:
Internal failure costs
This is where most manufacturers traditionally begin tracking CoQ. Internal failure costs arise when a product fails inspection or regulatory requirements. These failures are detected before reaching the customer. Examples include costs associated with:
- Scrap and rework
- Downtime and corrective actions
- Re-inspections
- Process troubleshooting
- Lost material
Though painful, internal failures are at least contained within the facility and do not yet impact the customer. Internal failures, however, can still significantly impact a business’ profit margins.
External failure costs
External failure costs are failures or defects that are not discovered until after the product has reached the customer. These types of costs can be most damaging to a company, both financially and reputationally.
Examples of these costs include:
- Product recalls
- Warranty claims
- Customer complaint handling
- Investigations and root cause analysis
- Regulatory fines
- Loss of customer trust or future business
In highly regulated industries where product failures can cause major detriment to consumers, an external failure cannot just trigger regulatory scrutiny, but also potential legal liability and safety concerns, making this the costliest type of quality failure.
How to calculate the Cost of Quality (CoQ)
The following simple formula can be used to calculate CoQ:
CoQ = CoGQ (Prevention + Appraisal) + CoPQ (Internal Failures + External Failures)
Example:
Quality Activity |
Monthly Cost |
Training Programs |
$4,000 |
Supplier Audits |
$3,000 |
In-Process Inspections |
$5,000 |
Scrap & Rework |
$15,000 |
Customer Warranty Claims |
$8,000 |
Audit Prep Time |
$2,500 |
Manual Documentation |
$3,500 |
Downtime from Issues |
$10,000 |
Total Cost of Quality |
$51,000 |
Hidden costs of quality that manufacturers overlook
Most organizations focus heavily on internal and external failure costs – the costs associated with poor quality - because they are straightforward and easier to measure. But this narrow view can lead to a false sense of control. Below are some often-overlooked quality-related costs:
Inefficient change management
Poorly managed change processes, such as delays in implementing engineering changes or updating documents, can stall production and lead to inaccuracies and compliance gaps.
Audit preparation time
Manually gathering documentation and records for audits (internal, customer or regulatory) consumes valuable staff time, especially when documentation is difficult to track down.
Training gaps
Incomplete or outdated training can lead to mistakes, especially in complex production environments.
Nonconformance backlogs
Unresolved corrective actions or overdue nonconformance reports create bottlenecks that delay production and increase risk by hindering the implementation of effective corrective and preventive actions.
Supplier quality issues
Poor visibility into supplier performance can lead to the need for increased inspection efforts, material delays or downstream failures.
Compliance risks
Missed regulatory deadlines or data integrity issues, such as unverified signatures or incomplete traceability, can trigger costly findings during audits or inspections.
Manual processes
Quality teams using manual processes like spreadsheets, local file storage or multiple disconnected systems, significantly increase labor costs and the risk of errors.
Why understanding total cost of quality matters
Companies must understand the total cost of quality (TCoQ) to get a realistic and complete financial picture of how all quality efforts impact the bottom line. Analysts must look beyond obvious costs, like scrap and rework, to understand the cost of less visible quality inefficiencies, including production downtime, engineering errors or improper customer complaint handling.
Here’s why it matters:
Reveals true cost drivers
Without a full CoQ analysis, manufacturers may focus only on surface-level issues, like defective products, and miss deeper problems, such as poor process design, inefficient training or supplier inconsistencies. Understanding total CoQ helps pinpoint where resources are being wasted.
Supports smarter investment decisions
Knowing how much you're spending on prevention, appraisal and failures, both internal and external, helps justify company investments in equipment and processes that can have a huge impact, such as improved automations, additional training or new software. It gives leadership data to back up quality improvement initiatives with ROI projections.
Strengthens regulatory compliance
In industries like aerospace and life sciences, failing to manage the hidden costs tied to compliance, such as documentation gaps or audit prep time, can result in fines or failed audits. Tracking total CoQ helps maintain readiness and reduce risk.
Improves profitability
By identifying and eliminating hidden quality costs, such as downtime, overtime labor or warranty claims, manufacturers can improve operational efficiency and reduce expenses, directly improving profit margins.
Drives continuous improvement
Insight into total CoQ provides a measurable baseline for ongoing quality improvement efforts. It helps teams track whether process changes are reducing costs and increasing customer satisfaction as planned.
How QMS software reduces the cost of quality
A modern, cloud-based QMS solution like QT9 QMS empowers organizations to go beyond tracking rework and scrap. It gives them the tools to identify, analyze and eliminate hidden costs through:
Real-time visibility
A modern QMS enables quality teams to monitor key metrics, trends, nonconformances, supplier performance and more in real time. Early issue detection helps prevent small problems from becoming costly failures.
Automated workflows
QMS software replaces spreadsheets and manual processes with automated, trackable systems for document control, audit management, training tracking, equipment calibration and more. This saves time, reduces inaccuracies and improves consistency across processes.
Streamlined Corrective and Preventive Actions (CAPA)
QMS software ensures that corrective actions are properly documented, assigned and resolved on time. It connects CAPAs to related audits, complaints or nonconformances, creating full traceability and preventing repeat issues, reducing the risk of recurring quality problems.
Enhanced training management
Automated training modules ensure that employees are always trained and qualified for their roles. Built-in tracking and reminders eliminate missed certifications or outdated procedures.
Stronger supplier quality control
With QMS software, you can monitor and evaluate supplier quality, track incoming inspection failures and complaints to strengthen your supply chain and lower external failure costs.
Easy reporting and dashboards
Use built-in dashboards to track key metrics like cost of quality over time, on a per-site or global level, enabling data-driven decision making.
Data-driven continuous improvement
Visible, real-time analytics help quality leaders identify cost drivers, and track the effectiveness of improvement efforts. Quality training programs build workforces skilled in quality principles and practices
Understanding total CoQ for targeted improvement
If businesses only track obvious costs like scrap or failed inspections, they're only seeing the tip of the iceberg. The true cost of quality includes every hour, dollar and opportunity lost to inefficiencies across the quality ecosystem. By taking a holistic approach, businesses can turn their quality program into a proactive, value-generating force.
In a world where manufacturers face tighter margins as well as greater public and regulatory scrutiny, quality is becoming more than a function of compliance but also a driver of the bottom line.
Organizations that consider quality an investment and not simply a cost are better positioned to increase efficiency and deliver consistent customer satisfaction. By understanding and tracking the total cost of quality, quality leaders can:
- Make better resource allocation decisions
- Prioritize process improvements with measurable ROI
- Justify quality investments to executive leadership
- Strengthen competitive advantage through consistent performance
Ready to reduce the Cost of Quality?
Explore how QT9 QMS can help your organization identify hidden costs, improve processes and boost compliance while driving down the cost of quality. Request a free demo to see how QT9 QMS can reduce your cost of quality.
FAQ: Cost of Quality Explained
What is the Cost of Quality (COQ) in manufacturing?
The Cost of Quality in manufacturing is the total cost to ensure products meet quality standards, including prevention, appraisal and failure costs.
What are the four categories of COQ?
- Prevention
- Appraisal
- Internal Failure
- External Failure
How do you calculate COQ?
CoQ = (Prevention + Appraisal) + (Internal Failure + External Failure)
How can QMS software reduce CoQ?
QMS software reduces CoQ by automating manual processes, improving visibility and reducing compliance risks.
Share this
- QT9 QMS (26)
- QT9 ERP (16)
- QT9 MRP (13)
- Company News (7)
- Medical Device (7)
- MRP Manufacturing (6)
- QMS Manufacturing (6)
- Document Control (5)
- Inventory Management (5)
- Pharma (5)
- FDA Compliance (4)
- QMS Life Sciences (4)
- CAPA (3)
- ISO 9001 (3)
- QMS Supplier Management (3)
- Accounting (2)
- Bill of Materials (2)
- Change Control (2)
- EBRs (2)
- ERP Life Sciences (2)
- FDA 21 CFR 820 (2)
- ISO 13485 (2)
- ISO Compliance (2)
- AS9100 (1)
- Aerospace (1)
- Analytics & Reporting (1)
- Audit Management (1)
- Calibrations (1)
- Cosmetics (1)
- DHF/DMR/DHR (1)
- Design Controls (1)
- ERP Manufacturing (1)
- Inspections (1)
- MoCRA (1)
- QMSR (1)
- Quality Events (1)
- Risk Management (1)
- August 2025 (8)
- July 2025 (6)
- June 2025 (7)
- May 2025 (5)
- April 2025 (2)
- March 2025 (4)
- February 2025 (4)
- January 2025 (6)
- December 2024 (4)
- November 2024 (4)
- October 2024 (5)
- September 2024 (3)
- August 2024 (3)
- July 2024 (3)
- June 2024 (5)
- May 2024 (3)
- April 2024 (3)
- March 2024 (3)
- February 2024 (5)
- January 2024 (3)