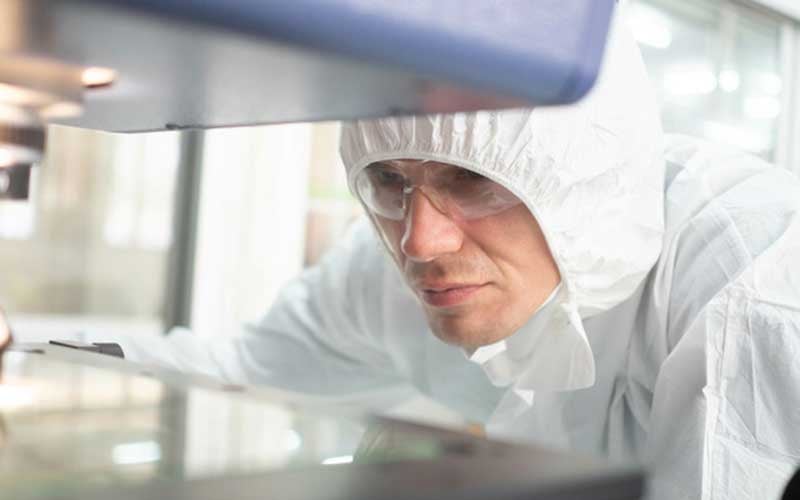
"You guys include everything. I am using modules I didn't expect to use."
- Peter Wysgalla
Global Quality Manager
Manufacturing and lab quality
You may have never considered the effects of indirect sunlight on the safety of your car’s seatbelt. But thankfully, automotive manufacturers have made it a point to do just that, and they know where to turn to get that information.
Often they look to Atlas Material Testing Solutions, a leader in materials testing offering a full line of weathering testing instruments, as well as laboratory and outdoor testing services. Their products test the effects of natural and artificial light, fire, water, chemicals and more on almost any type of product, from paint and textiles to electronics components.
Atlas has offices and customers around the world. So it is important that they comply with international quality and safety standards, particularly ISO 9001 for overall quality management and ISO 17025 for testing and calibration laboratories.
Ability to scale
As a company that must stay on top of technology in many industries, Atlas is continually improving upon their own products and services. In 2013 Atlas took steps to automate its quality management processes. The quality control system in place at the time was all manual, utilizing mostly Excel spreadsheets and Word documents.
Atlas chose to automate quality control processes with QT9 QMS based on the ability to centralize data while remaining affordable. Streamlining document control and corrective actions was the first objective, with the goal of scaling into other modules shortly after.
Since implementing QT9, Atlas has integrated several of the 25 modules that come standard in the QT9 QMS platform, utilizing modules beyond their initial expectations. Over the years, they have nearly doubled their concurrent licenses. This has enabled them to establish a robust multi-site quality system that serves their international operations on a daily basis.
CAPAs and NCPs
The company was quickly able to create efficiency in its corrective actions processes by using the eQMS to automatically reassign CAPAs globally to the right people. Peter Wysgalla, Atlas Global Quality Manager, outlines some of the initial successes with the QT9 eQMS. “The automatic review dates feature for documents and gauges has been key,” he says. “It seems simple, but as soon as you finish an audit the system schedules the next one for the following year and it’s in the system and ready to go when auditors want to see your audit schedule.”
A few years ago, Atlas decided to integrate its nonconforming products (NCPs) into the QT9 QMS. Now whenever a part fails during the manufacturing process, it is tagged with an NCP in the eQMS. NCPs are reviewed daily in a meeting between the quality, purchasing and engineering teams, and a course of action quickly determined. The notify supplier feature further enhances the process by involving suppliers when necessary.
“In 10-15 minutes, we can handle all of our material,” explains Wysgalla. “Everything is tagged with a QT9 NCP, so we can trace it back and act appropriately.
"It wasn't obvious how valuable this would be at first, but now that we've implemented it and involved our suppliers, it's become an important tool for maintaining our NCPs," adds Wysgalla.
Training, audit management and FEMA
Other modules that Wysgalla and his team have found helpful for simplifying quality efforts are the Training, Audit and FMEA modules. The Training Module allows them to educate service techs around the world via the quality software, tasks that used to be paper-based. The Audit Management Module has allowed the company to dispense with the hiring of third-party auditors since audits are now managed through the QT9 software.
“I always get a positive citation in an audit, especially with the links QT9 provides to all of the other modules,” says Wysgalla. “If audits are done virtually, I can be in my office and show a document, a gauge record, etc., in a matter of seconds. It has really made audits easy.”
Challenge
Atlas Material Testing Solutions, dedicated to maintaining its ISO 9001 and 17025 certifications, wanted an eQMS solution that offered immediate efficiencies and the opportunity to implement additional process improvements in the future.
Solution
Atlas looked to QT9 for a cost-efficient QMS that was easy to adopt, quick to implement and ready to use out of the box.
Results
Atlas implemented QT9 QMS within six months, achieving a complete overhaul of their quality system for enhanced efficiency, and has taken advantage of almost all of the system's 25 modules.
About Atlas Material Testing Solutions
Atlas Material Testing Solutions is a leader in materials testing offering a full line of weathering testing instruments, as well as laboratory and outdoor testing services. Their products test the effects of natural and artificial light, fire, water, chemicals and more on almost any type of product, from paint and textiles to electronics components.