Industry
Fluid Systems & Services
Founded
1947
Location
Cleveland, OH
Employees
5,700+
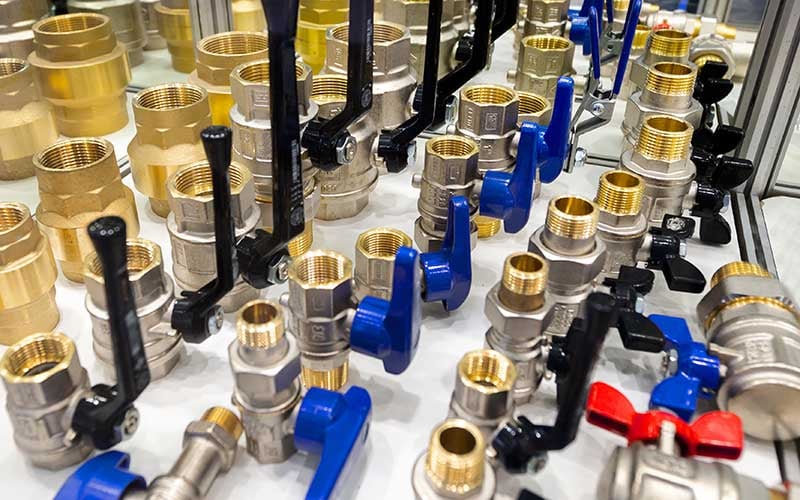
“The nice thing with QT9 is that we have access to everything, yet we didn't have to implement everything at once. This allowed us to grow into everything and utilize everything once we were ready."
- Jason Yamamoto
Operations & Service Manager
From Excel, Teams and Email, to one QMS software
Swagelok is a privately held developer of fluid system products, assemblies and services for the oil and gas, chemical and petrochemical, semiconductor, transportation, pharmaceutical, medical and transportation industries. Headquartered in the U.S. with more than 200 sales and service centers across 70 countries, Swagelok had been using a host of manual quality processes among their different locations, from Excel spreadsheets to files organized in Teams.
In 2018, quality managers at the Portland, Oregon, Swagelok Sales and Service Center (SSC) were looking for a solution that would allow them to better organize and automate their quality processes. They wanted a system that would seamlessly distribute ownership across the organization -- a system that not only offered everything they needed, but also allowed them to grow within it when they were ready.
While researching QMSs, the Portland location received a supplier corrective action automated message from one of its customers, sent via QT9 QMS. They were immediately intrigued and began investigating the platform. The customer invited them to visit their facility and see how they utilized QT9 QMS in real time. After that, as Jason Yamamoto describes, it was a “no brainer."
Yamamoto, Operations and Service Manager for two Swagelok SSCs in Australia/New Zealand, was working in the Portland office at the time. "The real benefit we saw from Portland was our ability to get away from all the spreadsheets and manual quality management processes," he says. "You can really spread ownership across the organization by enabling different people to login, create tasks and assign tasks to different team members."
After using QT9 QMS for three years at the Portland office, the team there was able to convince Swagelok Corporate to adopt QT9 eQMS as the standard for their distributor functions. Since then, 18 additional Swagelok distributors and SSCs have implemented QT9 QMS, not only in the United States, but all around the world.
Audit success = customer success
Since 1947, Swagelok has prided itself on helping customers achieve their goals by delivering the best products and services with integrity. The ultimate goal of automating their quality processes was to further that mission by reducing or eliminating regulatory and customer audit findings.
The Swagelok distributorship based in Alpharetta, Georgia, began implementing the QT9 system in 2022. Alpharetta Quality Manager Louis Sapic says, "Prior to that, everything was a hodgepodge of local documents, and we were just trying to control them. Engineering changes, calibrations, PMs, they were just kind of all hidden away. We had audit findings over the years for things just not getting done or lost in the weeds, because there was not a good repository for everything."
QT9’s Document Control module and its links to other quality control modules helped solve the distributor’s problems. “We had an auditor come in for one of our customers,” says Sapic. “He scheduled a day and a half to audit, and we just blew right through it because of QT9.”
Yamamoto shares a similar story. “In Portland, we had the same ISO auditor for seven years,” he recalls. “She was extremely complementary of the [QT9] system. How accessible, how quick, how everything kind of tied together. You could see an audit; you could see the corrective actions from the audit. You could see the root cause analysis; you could see the preventive actions, the opportunities for improvement. Everything was tied together in the system. And the last audit that she did for us, we had no corrective actions.”
Scaling for continued success
Swagelok offices have been able to implement additional QMS modules on their own timeline, thanks to the scalability of the QT9 QMS model. The Australia/New Zealand office, for instance, identified one or two modules to implement each quarter. They've implemented Preventive Maintenance, Calibrations, Nonconforming Products and other ISO functions, among others.
“The nice thing with QT9 is that we have access to everything, yet we didn’t have to implement everything at once,” notes Yamamoto. “This allowed us to grow into everything and utilize everything once we were ready.”
Consistent formatting across the QT9 quality management system has made rolling out new modules simpler. “They are all structured the same,” notes Sapic. “So, once you learn one module, it is very easy to pick up everything else.”
Boutique-level customer support
QT9 has been there to assist Swagelok offices with the implementation and rollout of additional modules. Swagelok offices have taken advantage of the hands-on implementation support, training and the accessibility of QT9 customer interaction specialists. “The support has been amazing,” says Yamamoto. “We feel like it has really has been catered to us.”
Martin Ehlert, Quality Manager for Swagelok's Sales and Service Center in the Netherlands, says, "What surprised me was the ease of working with QT9. It was very easy for me to get the modules up and running and implement everything. We have made big improvements in document management and the handling of our corrective and preventive actions just because we started using QT9. And the visibility of the status of corrective actions and audits is much easier to present to management.”
Ehlert brings Swagelok’s experience with QT9 QMS full circle – drawn from a need for better document management to general work process improvements and information flow all the way to the top. “We have made big improvements in document management and the handling of our corrective and preventive actions just because we started using QT9,” says Ehlert. “The visibility of the status of corrective actions and audits is much easier to present to management. Just from a quick moment’s glance, he now has a much better idea of all that is happening within the quality management system.”
"I couldn't imagine life without QT9," says Yamamoto. "QT9 has become an integral part of the company, not only for me, but also everyone else."
Challenge
Swagelok offices in Portland, Oregon, were looking to automate quality processes kept in spreadsheets. They wanted a solution that would enable them to distribute quality ownership across the organization and give them scalability to grow.
Solution
Swagelok Portland chose QT9 QMS after seeing how well it worked for one of its customers. QT9 QMS provides a quality management software with virtually unlimited scalability.
Results
Today Swagelok corporate has adopted QT9 QMS as the standard for their distributors. Over 19 Swagelok sales and service centers around the world are using the QT9 QMS platform.About Swagelok
Swagelok is a privately held developer of fluid system products, assemblies and services for the oil and gas, chemical and petrochemical, semiconductor, transportation, pharmaceutical, medical and transportation industries. Headquartered in the U.S. with more than 200 sales and service centers across 70 countries, Swagelok had been using a host of manual quality processes among their different locations, from Excel spreadsheets to files organized in Teams.
"QT9 has become an integral part of the company, not only for me, but also everyone else."
- Jason Yamamoto
Operations & Service Manager