Voyant Beauty Invests in Innovation with QT9 Quality Management Software
For Voyant Beauty, helping clients speed products to market means harnessing innovation to the best of their abilities. That's why when they saw a need to centralize and streamline quality processes, they looked to automate with QT9 QMS.
Industry
Personal Care and Beauty Products
Founded
2017
Location
HQ: Chicago, IL., additional locations in the U.S, Canada, and Europe
Employees
3,000+
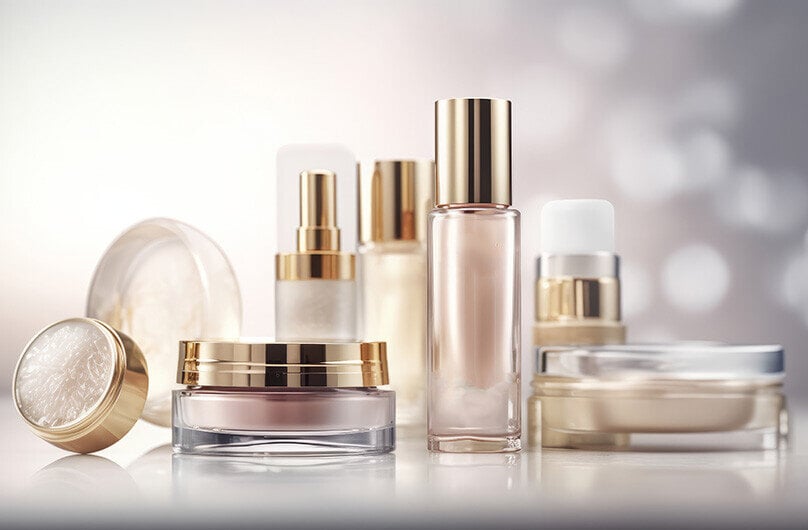
“I knew immediately that it was something people could learn and adopt quickly. ”
- Kimberly Patchak
Senior director of corporate quality systems and regulatory
Voyant Beauty case study
Voyant Beauty, a contract manufacturer of personal care and household products, prides itself on harnessing innovation to help clients speed products to market. After a series of acquisitions, company management was looking for a way to standardize and centralize data across locations and get greater transparency into operations and compliance activities. They decided to lean into their innovative roots and began considering automated quality management system (QMS) solutions that would best support customer outcomes.
QT9 QMS was at the top of the list, given its intuitive interface, extensive capabilities and concurrent licensing structure. Since implementing QT9 QMS in 2021, Voyant has reduced process times at least 50 percent, freeing up employees to focus on more impactful tasks. With a significant decrease in cycle times, customer satisfaction has grown. As hoped, now Voyant’s regulatory needs are met more accurately and systematically and with greater visibility, minimizing the risk of noncompliance.
Centralizing and streamlining quality
“Most of our sites were using manual systems,” says Kimberly Patchak, Senior Director of Corporate Quality Systems and Regulatory at Voyant. “It was difficult to see what was happening at the site level because processes were being managed within paper logs. Paperwork would get lost waiting for a physical signature. Every site was numbering records in a different manner, so there was no uniformity. It was kind of a mess.”
As with many new eQMS customers, Voyant began use of QT9 QMS by implementing the document control module. Where once each site had its own document storage location, today every department and every site in the company has access to documents via one, centralized location. The company has taken full advantage of its capabilities.
“We use Document Control every day, for everything from corporate policies and procedures, to site-level procedures and instructions, to guidance documents and records,” says Patchak. “Of course we use it for document updates and reviews. We also use it to manage our quality agreements with customers, which is amazing.”
More recently, Voyant employees implemented the Nonconforming Products and Corrective Actions modules, along with the Supplier Management modules. “The supplier database is very important, because it is basically our approved supplier list,” says Patchak. “It is great because we can put in service suppliers, which are not captured in our ERP system. We can have an approved supplier list and an approved supplier list with materials.”
Complementing those processes is the QT9 QMS Supplier Portal, which Voyant uses to initiate and monitor supplier communication. “With the implementation of the Corrective Actions module, we started using the portal to issue supplier CARs [Corrective Action Reports]. It has made the process and communication with them much easier.”
Scalability, support and training
Since initially implementing QT9 QMS, Voyant has changed its strategy for module use based on needs, keeping customer interests in mind. “We have really tried to focus on the things that will help our employees at the manufacturing sites do their jobs more easily,” notes Patchak. “Another goal has been getting greater visibility into whether or not things are going well at each site.” Currently Voyant is rolling out the platform’s Deviations, Training and Audit modules.
Even if there are no current plans to implement a module, if a department or site presents a need, Patchak is supportive of them implementing a module on their own. “They develop their procedures, do all of the upfront work and test it, and I help implement it when its ready,” says Patchak. “That flexibility has been really helpful.”
Beyond scaling operations and compliance modules to their needs, Voyant has taken advantage of QT9’s unlimited support and training to help ensure a smooth rollout and faster user adoption. QT9’s support team developed an implementation plan based on the company’s goals, and has continued to assist in modifying the plan as goals have changed. Patchak notes that multiple employees have completed live or recorded trainings. “The support has been really important to us,” says Patchak. “Myself, being the administrator, I really appreciated the ability to have an expert to meet with and make sure I wasn’t doing something wrong.”
Intuitive interface
Patchak first learned of QT9 QMS at a tradeshow and liked its intuitive user interface right away. “I knew immediately that it was something people could learn and adopt quickly,” says Patchak. “I like that the system is robust and customizable, but not too customizable to make it complicated for our users. The really big sell was that we could have unlimited users. That was great for us because we wanted everyone to be able to access it.”
Voyant utilizes unlimited QT9 QMS licenses, with the system in use at all 11 sites as well as at its research and development arm, Atelier. Voyant has made the use of the QMS mandatory for certain departments, such as quality control, but has found that many others have begun to take advantage of the software’s capabilities, including the finance, engineering, laboratory and procurement departments.
Continuous improvement throughout
Patchak’s favorite part of her position as quality director is seeing the continuous improvements taking place at Voyant, especially those making processes more efficient and easier. “QT9 has helped by ensuring that we have uniform processes and that we have one place where we document and store information. It also provides us the opportunity to look at data and conduct data analysis. So we have total visibility into operations and compliance in real time.”
Voyant Beauty's adoption of QT9 QMS software and subsequent streamlining of quality management processes across locations is another example of the company’s commitment to quality and innovation. By leveraging the system's capabilities, Voyant has not only enhanced operational efficiency but also improved compliance and customer satisfaction.
The intuitive interface and flexibility offered by QT9 QMS have empowered employees to implement and manage processes more effectively, ensuring uniformity, transparency and compliance. As Voyant continues to scale and evolve, their commitment to innovation positions them to maintain high standards in quality while serving customers with efficiency and expertise.
Challenge
Create visibility across locations to more easily manage process health and identify potential quality issues.
Solution
Find an eQMS to replace manual and nonperforming electronic methods, uniting documentation and processes in one system used by all locations.
Results
- 50 to 80 percent reduction in document change and approval times
- Significant decrease in cycle time, creating greater customer satisfaction
- Ability to initiate quality system health checks and minimize risk of noncompliance
About Voyant Beauty
Voyant Beauty, a contract manufacturer of personal care and household products, prides itself on harnessing innovation to help clients speed products to market. After a series of acquisitions, company management was looking for a way to standardize and centralize data across locations and get greater transparency into operations and compliance activities. They decided to lean into their innovative roots and began considering automated quality management system (QMS) solutions that would best support customer outcomes.