Industry
Telecommunications
Founded
1971
Location
International
Employees
1,500+
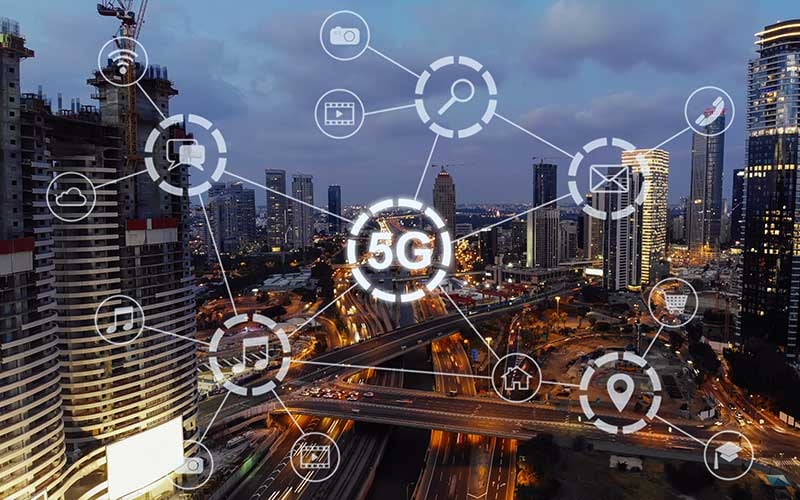
"QT9 is a holistic electronic management system solution that can organize your business for ease of compliance as well as your own internal processing."
- Anthony Lenarz
Global quality system manager at Dura-Line
Connecting and centralizing quality metrics
Dura-Line is a global manufacturer and distributor of high-density polyethylene (HDPE) conduit for the telecommunications industry. The company’s products are used to protect critical infrastructure across the globe, including fiber optic and power cables.
After Dura-Line was acquired by new global parent, Orbia, several business units were restructured under the Dura-Line name, bringing together 20 sites located all around the world. When they merged, quality control activities for the sites were being managed using mostly SharePoint platforms established on local hard drives, and data control was all over the place. Dura-Line quality control managers embarked on a journey to find one centralized quality management system that could easily be implemented across all locations.
“From internal audits to corrective actions to management review, there was no centralized management system structure across all the sites,” says Anthony Lenarz, Global Quality Systems Manager for Dura-Line. “We had to harmonize the business process, the quality management system, and consolidate our document information in one central location to improve overall management.”
More for the money
In their search for a solution, Dura-Line’s quality control managers knew they needed a QMS that addressed specific criteria. In terms of day-to-day management, those were document control, internal audit management, and corrective actions management. Ease of use and affordability were also essential. The company ultimately decided on the QT9 eQMS platform, citing:
- Quick deployment
- Out-of-the box functionality
- Intuitive user interface
- Relative affordability
- ISO 9001 compliant
“One of the big drivers for using QT9 was that it didn’t require a whole lot of customization to fit the needs of Dura-Line,” says Lenarz. Even though QT9 QMS is an out-of-the box solution, Dura-Line quality experts liked that it is diverse enough to address so many aspects of their quality management needs, offering more than 25 different scalable modules at no additional cost.
Functional modules
The number of solutions offered combined with the functionality of the QT9 QMS platform are the fuel driving the system’s usefulness for Dura-Line as they take full advantage of all it offers.
Document control is among the modules that is used by Dura-Line on a daily basis. “If I’m not looking at revisions or approvals for documents, I’m always checking the new document queue,” says Caylin Cox, Quality Management Systems Engineer for Dura-Line. She notes that document control, audit management and corrective actions capabilities are key to their management system. She also looks to the subtask capabilities of the system to keep her on track with outstanding projects.
While each Dura-Line site maintains its own internal audits, Lenarz and Cox oversee those audits through the QMS and are able to follow up with support of corrective actions, verification of effectiveness and then closure.
“Across the organization, the document control module is the number one most frequently used,” says Lenarz. “Supplier corrective actions is number two, then just general corrective actions, number three. Internal audits and calibrations fit in around four and five.”
Easy deployment
With dedicated customer support and an intuitive user interface, Dura-Line was quickly up and running with the QT9 software. “It was a flawless deployment of the system because the intuitive nature made rollout of the software easy,” recalls Lenarz. “Once you understand the inner workings of one module, you can rapidly deploy that knowledge across any aspect of the QT9 QMS. Its intuitiveness made the rollout exceptionally quick and the adoption very fast across the organization.”
During implementation, Dura-Line was able to take full advantage of QT9’s customer support program, which offers unlimited training for initial setup as well as ongoing maintenance and support. “In my experience with QT9, what stands out the most is the exceptional customer service and support,” says Cox. "You were constantly accessible. You were there at any point that we needed support."
Audit success
Dura-Line has seen a substantial reduction in internal audit findings, which ultimately translates to less time and effort spent on correcting issues and more time spent on furthering quality process effectiveness across the organization. “We went from having no certification, to achieving the certification of both ISO 9001 and TL 9000, with praise from external auditors," says Lenarz. “In some of our recent external audits, auditors have praised the ease of using QT9 and the overall implementation of it.”
Challenge
Dura-Line needed to establish a cohesive quality management system across 20 global sites in the most efficient and cost-effective manner.
Solution
Dura-Line chose QT9 QMS based on affordability and out-of-the-box capability.
Results
The telecom supplier was able to link all offices under one management system within a year.About Dura-Line
Dura-Line is a global manufacturer and distributor of high-density polyethylene (HDPE) conduit for the telecommunications industry. The company’s products are used to protect critical infrastructure across the globe, including fiber optic and power cables.