CAPA Management Software to Fix and Prevent Quality Issues
Automate corrective and preventive actions with built-in workflows, root-cause tools and full traceability to meet FDA and ISO standards.
Close Issues Faster
Automate CAPA tracking for faster issue resolution.
Ensure Compliance
Meet FDA, ISO & GMP standards with audit-ready CAPA records.
Central CAPA Database
Store corrective and preventive actions in one searchable hub.
Root-Cause Analysis
Use 5 Whys or Fishbone tools to locate and address problems.
Automated Task Alerts
Stay on track with CAPA alerts and reminders
Link CAPAs to Audits
Link CAPAs to audits for full traceability.
What is CAPA management software?
CAPA management, short for Corrective and Preventive Action, is the process organizations use to investigate the root causes of quality issues, implement corrective actions and prevent recurrence. It is a critical part of quality management systems and required by regulatory standards like ISO 9001, FDA 21 CFR Part 820 and GMP to ensure continuous improvement and regulatory compliance.
QT9’s CAPA management software streamlines the way businesses manage and resolve issues. From initiating a CAPA and assigning tasks to documenting root-cause analysis and verifying effectiveness, QT9 automates every step of the process. Fully integrated within QT9 QMS, it connects with audits, nonconformances and customer complaints, ensuring faster resolutions, better visibility and complete traceability across your quality system.
A comprehensive CAPA software solution
Free up time with corrective actions tools built in to QT9 QMS.
Manage Approvals
Assign approver/s and approve, reject or verify corrective actions.
Email Alerts
Send users email alerts and reminders based on your settings.
Real-Time Reporting
Track corrective actions by any field. Create charts and export reports to Excel.
Paperless Made Effortless
Easily export and email copies of corrective and preventive actions.
Verification of Effectiveness
Schedule verification of effectiveness after final approval.
User-Defined Fields
Create unlimited custom fields for tracking company-specific information.
Overdue Alerts
Initiate automated email alerts when CAPAs are overdue.
Unlimited Attachments
Attach unlimited files to any corrective or preventive action.
Manage Priorities
Set priority levels for CAPAs based on due dates within your organization.
Root Cause Analysis
Fully integrated Root Cause Analysis (RCA).
8D CAPA Process
The eight discipline problem-solving method is included.
Supplier Web Portal
Assign corrective actions to suppliers via the QT9 QMS Supplier Web Portal.
Unlimited Tasks
Types & Categories
Multiple Integrations
Integrated CAPA software
Automatically create corrective actions from multiple QT9 QMS integrated modules.
Customer Feedback
Quality Events
Nonconforming Products
Audit Management
Management Review
Risk Management
Safety Management
Inspections
Centralize data with 25+ modules
FAQ: CAPA Management
Corrective and preventive action, commonly called CAPA, is a methodical system used by businesses and manufacturers to identify the source of actual or potential problems and their root causes, determine solutions for problems, implement solutions and document each step to ensure a problem does not occur in the future.
Despite CAPA often being used as a catch-all term to refer to the overall process, corrective actions and preventive actions occur at different stages of a product’s lifecycle. Still, they are generally addressed in the same way.
Corrective Actions are the steps taken to identify and eliminate the cause of a nonconformity that has already occurred.
Preventive Actions are the steps taken to find and rectify the cause of a potential nonconformity to prevent it from occurring.
Nonconformity, also called nonconformance, is when a product or service deviates from a specification, standard or expectation so that the end result does not meet requirements.
The CAPA process can be very involved depending on your business and/or the nonconformity it is addressing. In high-level, general terms, the CAPA process involves:
- Identifying and describing the problem or nonconformance
- Taking any immediate actions necessary
- Investigating the root cause of the nonconformance
- Creating an action plan to address the root cause
- Implementing and then assessing the plan
- Communicating the new process
It is important to document each step of the CAPA process for review and future improvement purposes.
Root cause analysis (RCA) refers to efforts undertaken to identify the real cause of a nonconformance or quality problem. Popular root cause analysis models include Five Whys, Fishbone Diagrams, Failure Mode and Effects Analyses (FEMA), and Pareto Charts.
FDA 21 CFR 820 calls for regulated organizations to establish and maintain procedures for implementing corrective and preventive actions. Companies must be able to demonstrate a well-thought-out process, including methods for data analysis, root cause analysis, verification or validation of corrective or preventive actions, implementation of changes, keeping a record of changes in methods and procedures, and communicating relevant changes to management and others directly responsible for ensuring quality of the product.
ISO and GMP share CAPA standards with the FDA, however, documentation of the problem and how it was fixed is the only actual requirement.
Ultimately, companies need to be able to demonstrate to auditors that their quality system can effectively identify problems quickly and implement effective corrective and preventive actions.
QT9 QMS has 25+ interconnected modules that come standard, including a CAPA module that connects with other key applications, including audits, risk management, customer complaints, deviations and supplier management. It’s cloud-based platform allows you to keep track of corrective actions and synchronize records with anyone, anywhere.
QT9’s QMS software is a highly rated, affordable, easy-to-use quality management system that excels at all of the processes that go into providing high-quality goods and services that are FDA and ISO compliant.
With QT9 QMS you get unlimited scalability and traceability at a great price, so you can bring quality products and services to market in the most efficient way.
Additional quality resources
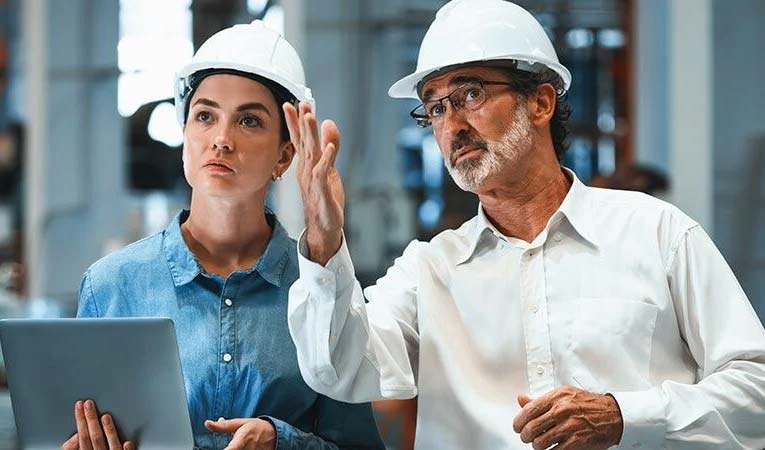
CAPA Management Software for Efficient Compliance
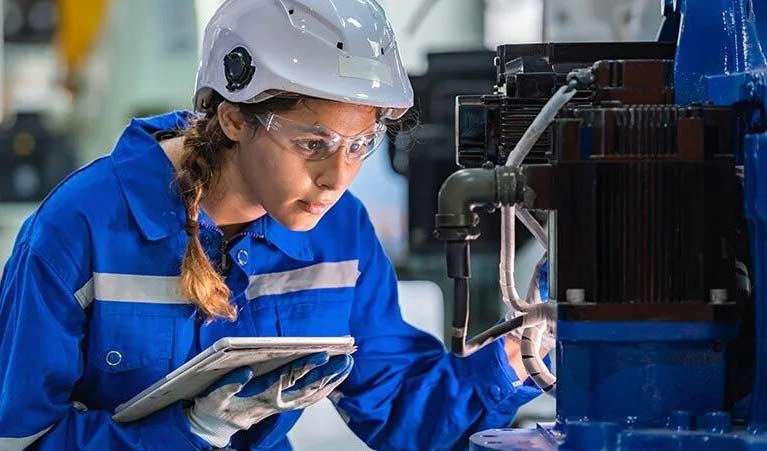
Best Practices for Nonconformance Management
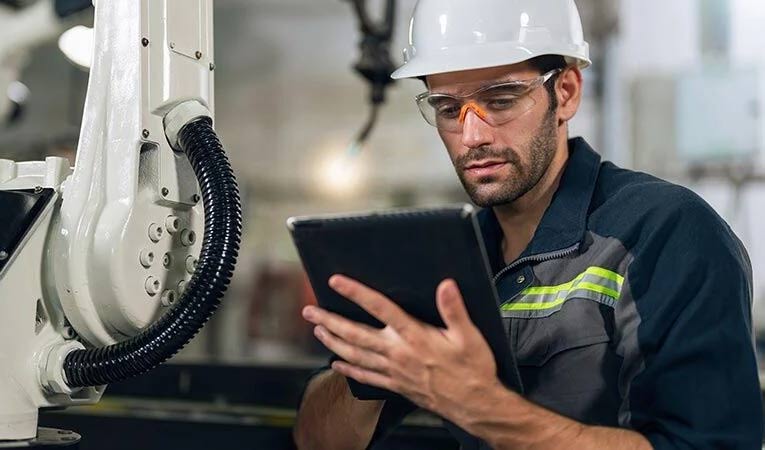
Best CAPA software in 2024
Try QT9 for free
Ready to simplify your quality processes? No credit card needed.